Sensors, data loggers, automation
News
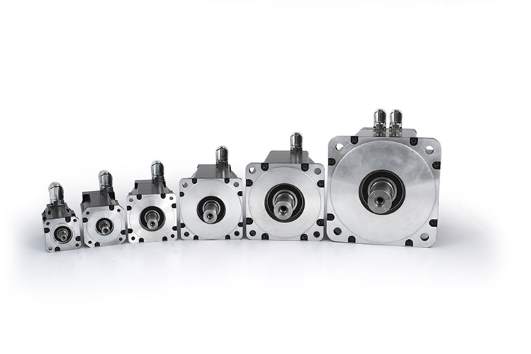
New Max Jac® IP69K electric linear actuator delivers reliable and robust performance in rugged applications
Thomson’s newest release of a heavy-duty linear actuator, the Max Jac® electric linear actuator is designed for high performance in the toughest applications. It is built to work with virtually no maintenance while maintaining accuracy under the most harsh conditions.
The Max Jac actuator has a stainless steel adapter and extension tubes which prevent leakage and enable it to achieve IP69K protection class status.
The Max Jac actuator successfully completed the following rigorous tests without compromise in performance and accuracy:
- 500 hours of salt spray
- Exposure to aggressive substances such as fertilizers, acid, oil, grease and cleaning agents
- Rigorous vibration testing
- Extreme temperatures ranging from -40°C to +85°C.
Thomson has created an electric linear actuator designed specifically for rugged use in mobile off-highway applications such as: fertilizer or salt and sand spreaders, throttle control or seeding applications, plus a broad array of marine, offshore, rail, mining and other applications with significant wash down or exposure to aggressive substances.
Will the Max Jac fit into my application?
The Max Jac can be custom designed by Thomson engineers to accommodate the demands of your specific application.
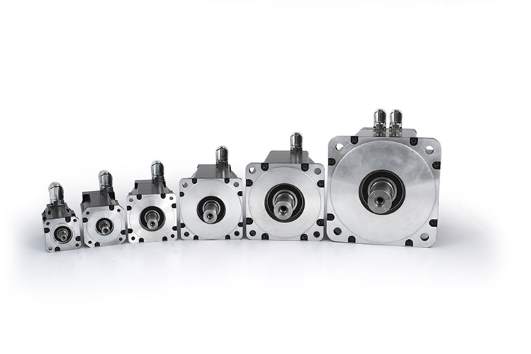
Streamlined Machine Design With New Thomson Glide Screw™
The Glide Screw™ is a breakthrough innovation from Thomson that combines the features of a linear bearing and a lead screw into one compact package. The patent-pending Glide Screw™ brings to you three tangible values: reduced footprint, improved equipment uptime, and lower cost of ownership.
■ Reduced footprint: Fewer components! – Integrated lead screw and linear bearing with no additional guidance needed.
■ Improved equipment uptime: Screw and linear bearing are already aligned.
■ Lower cost of ownership:
o Easy to install: Minimal prep time makes the install process fast.
o Minimal maintenance: Integrated Thomson Lube-for-Life lubrication block.
■ Custom configurations available: Special nuts, screw diameters and thread leads
available to accomodate your specific application.
Which applications are a great fit for the Glide Screw™?
The Glide Screw was designed to solve the challenge where smaller, cleaner, smoother, and quieter mechanical motion products are required, e.g.:
- 3D printing and engraving
- Fluid pipetting / 3-axis lab automation
- Test tube handling
- CD duplication
- Pick & place
- Syringe pumps
- In vitro diagnostics
- Medical imaging
- Many others!
The Thomson Glide Screw is genuine innovation, unique in motion control, and available now.
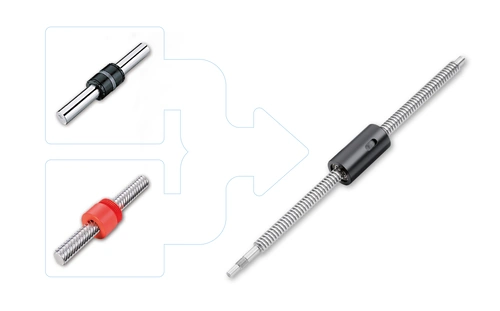
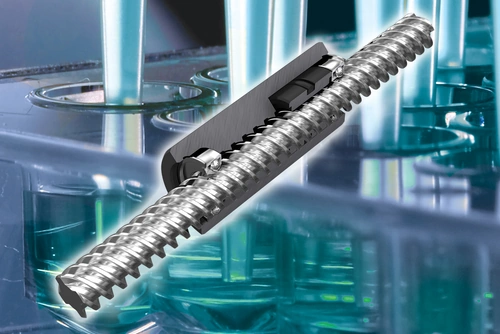
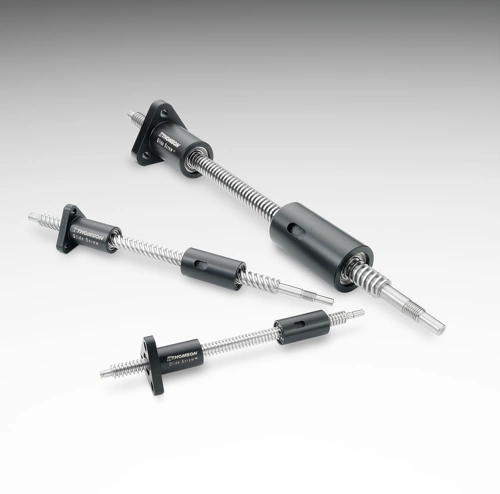
Going even further
Inobalt is looking forward to the new servo motors from KOLLMORGEN
“Smaller with more power. This is a very good combination with which we are now able to equip machines for increased productivity and more flexibly", Inobalt – manager Rolandas , Obsta has been appointed as the face of a new development of drive technology partner Kollmorgen. The possibilities offered by the second-generation servo motor AKM2G for Inobalt especially in the field of machine performance, have been reported to Mr. Obsta by the manufacturer.
In September, Kollmorgen hosted a partner event at its Ratingen European headquarters entitled "Together we can do more". The two-day event offered plenty of room for discussions with other contract partners and provided in-depth technical knowledge about today's automation solutions as well as the innovations of tomorrow. Partners from Europe and India did not miss the opportunity to gather know-how straight from the source. "We maintain a really close and cooperative relationship with Kollmorgen. In turn, this is a big plus for our customers", says Rolandas Obsta.
The second generation of AKM2G synchronous servo motors delivers up to 30% more torque, due to Kollmorgen’s expertise in developing and manufacturing compact, efficient motors that are powerful and highly configurable. Kollmorgen has succeeded in significantly reducing the winding losses, which directly improves the already efficient torque/revs ratio of existing AKM servo motors to date. "The second-generation AKM2G motors offer our partners more power with the same construction footprint," says Jan Treede, host and CEO of Kollmorgen Europe.
Kollmorgen's EU meeting gave first-hand information about the new generation of AKM2G motors. Inobalt – Manager Rolandas Obsta and Jan Treede CEO of Kollmorgen Europe, look forward to upcoming joint projects.
AKM2G Product Image
Smaller with more power: Kollmorgen has further increased the power density of the AKM2G servo motor.
Inobalt is looking forward to the new possibilities offered by the Kollmorgen AKM2G range of servo motors when in use.
ABOUT KOLLMORGEN
Since its founding in 1916, Kollmorgen’s innovative solutions have brought big ideas to life, kept the world safer, and improved peoples’ lives. Today, its world-class knowledge of motion systems and components, industry-leading quality, and deep expertise in linking and integrating standard and custom products continually delivers breakthrough solutions that are unmatched in performance, reliability, and ease-of-use. This gives machine builders around the world an irrefutable marketplace advantage and provides their customers with ultimate peace-of-mind. For further information please contact think@kollmorgen.com or visit our website www.kollmorgen.com/uk
Energy-saving made easy – Measuring energy efficiency in accordance with DIN EN ISO 50001
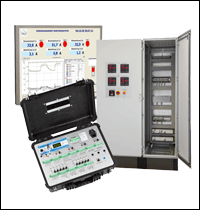
Saving energy is not just a priority for energy-intensive industries. Virtually any organisation is being forced to look at its energy efficiency. Furthermore, the DIN EN ISO 50001 standard (or the German SpaEfV legislation) makes the implementation of an energy management system inevitable in the long run.
We therefore apply our many years of experience in industrial measurement technology to advise and support you on measuring energy efficiency in accordance with EN ISO 50001 using our hardware and software products.
Our mobile energy measurement cases or stationary switch cabinet systems – both using Delphin hardware and software – identify and analyse potential energy savings and provide users directly with meaningful information.
The tried and tested data logger from Delphin's Message series is at the core of data acquisition systems already being used for energy management. The data logger can be connected with a 3-phase power measuring unit to acquire any required energy unit such as electrical power, active power, idle power, power consumption and so on. Measurement data processing and analysis then takes place independently within the data logger itself. The data is recorded to an internal memory and given a unique and manipulation-safe time and date stamp.
Our ProfiSignal software enables users to generate individual visualization interfaces to give a clear overview of a system and to enable easy operation as well as system auditing.
This enables compliance to DIN EN ISO 50001 and, for example, to the German legislation on energy efficiency (SpaEfV) and enables implementation of an energy management system in accordance with DIN EN ISO 50001.
Expert Logger – the latest generation of stand alone data loggers
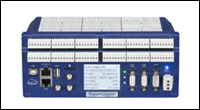
With its Expert Logger, Delphin Technology AG introduces a new generation of data loggers that combine the latest communication technology with advanced measurement technology. The device is being launched in three versions, capable of processing 16, 32 or 46 analog input channels. Upto 8 digital inputs/outputs and one SDI12 interface are also available depending on the version.
The main areas of application include product testing, environmental measurement technology, laboratory data acquisition, research and development, and trials and testing. All analog inputs are galvanically isolated from each other. A 24-bit A/D converter ensures fast,precision sampling rates of up to 50 measurements per second per channel. The devices are maintenance and noise free due to the absence of electromechanical components (such as relays) that are prone to wear and tear.
All Expert Loggers are equipped with internal 4 GB memories that can independently store up to100 million measurement values with date and time stamps. Storage capacity can be extended as required via external USB or LAN storage (NAS). Online measurement data or the contents of the data memory can be transmitted to the internet via an integrated WLAN or UMTS module.
The Expert Logger is also equipped with an energy-saving “sleep function“ for automated switching off during breaks in measuring. Independent operation is possible using batteries, rechargeables or solar panels. The Expert Logger can communicate as standard via CanBus, ModBus and ProfiBus. Internal software channels such as calculation channels, limit values and integrators enable online evaluation of measurements and the logging of meaningful data.
Users can quickly and effectively operate the Expert Logger using the powerful ProfiSignal Go software that is included free in delivery. ProfiSignal Go can be used to portray measurement data in trends and to carry out detailed analyses. The software also enables fast ASCII exporting of measurement data for MS Excel™ or for conversion into TDM format.
INOBALT Company representatives attended the conference "Mechatronics" in Latvia
3 of February representatives from company INOBALT at the invitation of Rezekne Higher Education (Rezekne, Latvia) participated in the traditional conference "Mechatronics".
During the conference INOBALT representatives presented their proposed products, services and solutions: electric linear actuators, mechatronics components, data loggers, process measurement solutions and automation systems.
The conference was attended by students and active teachers that are interested in the latest technologies and their applications.
After the conference there was a discussion, questions were asked, Rezekne Higher Education representatives presented their laboratories and under development prototypes. Inobalt representatives also adopted a rector and there were discussion about the possibilities of cooperation.
Moments of the Conference:
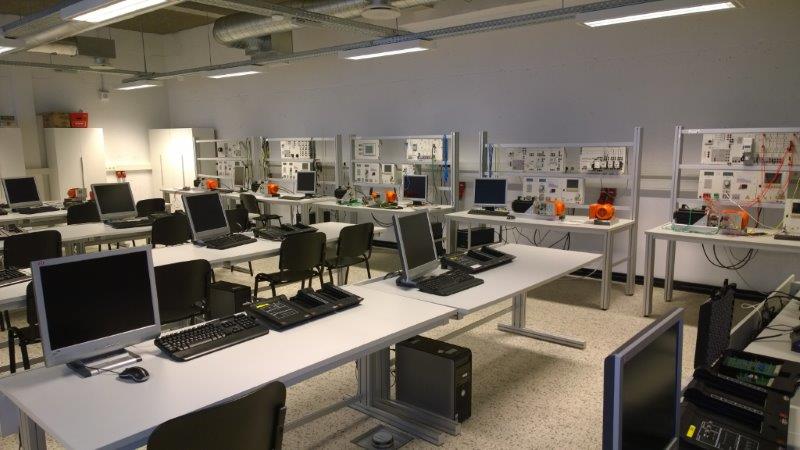
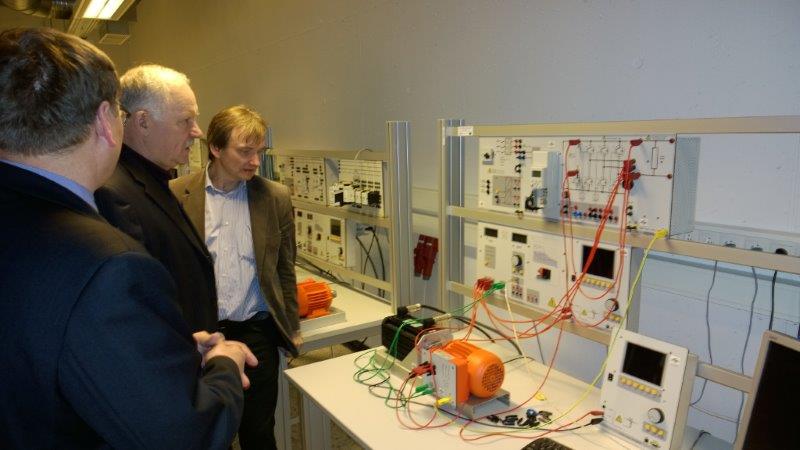
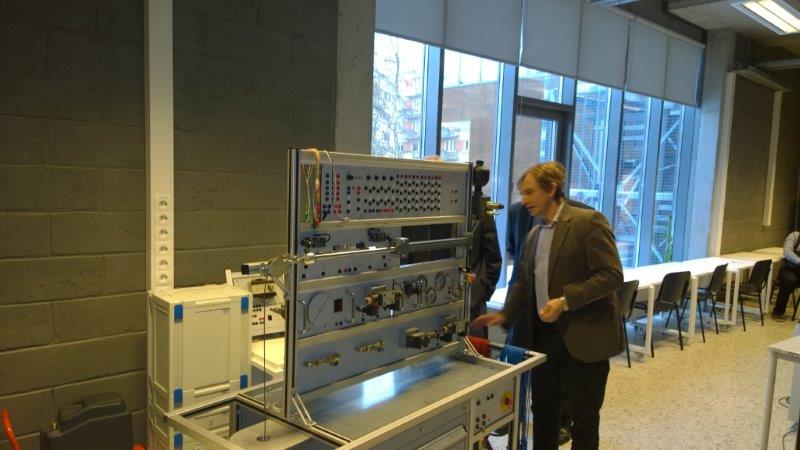
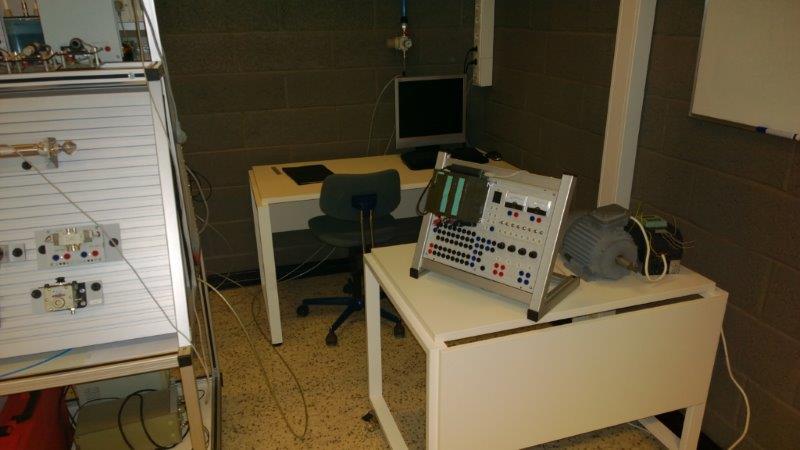
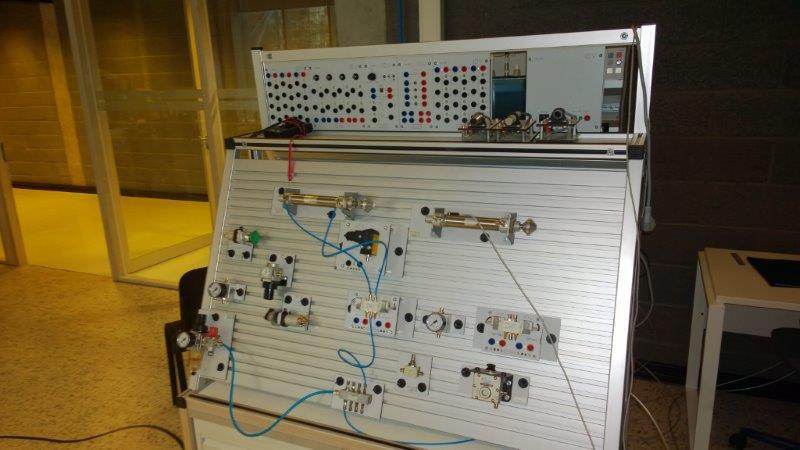
DS 500
Intelligent chart recorder for compressed air and gases
MEASUREMENT - CONTROL - INDICATION - ALARM - RECORDING - EVALUATION
Advantages:
![]() |
Clear layout: 7" colour screen with touch panel Versatile: Up to 12 optional sensors can be connected Easy: Very easy operation, automatic sensor identification Reliable: Stores all measured values reliably, 4 alarm relays for threshold exceedings Suitable for industrial applications: Metal housing IP 65 or panel mounting Data available though world wide web: Network-compatible and remote transmission via webserver Intelligent: Daily/weekly monthly reports Saves time and costs during installation |
From recording of the measured data, automatic sensor identification, indication on a big colour screen, alerting, storage up to remote read-out via webserver ... this is all possible with DS 500. By means of the CS Soft software alarms can be sent via SMS or e-mail. On the big 7" colour screen with touch panel all information are available at a glance. The operation is very easy. All measured values, measured curves and threshold exceedings are indicated. The curve progressions from the beginning of the measurement can be viewed by an easy slide of the finger.
Daily/weekly/monthly reports with costs in € and counter reading in m³ for each consumption sensor are completing the sophisticated system concept.
The big difference to ordinary paperless chart recorders reveals in the easy initiation and in the evaluation of the measured data. All sensors are identified directly and powered by DS 500. Everything is matched and tuned.
No time consuming studying of the instruction manual ... this saves time. Internal voltage supply of all sensors, no wiring of external mains units ... this saves additional costs.
By Kris Bagadia, PEAK Industrial Solutions
The statistics are startling. Up to 80% of Computerized Maintenance Management System implementations have failed in the past. When considering the costs associated with a CMMS project, an 80% failure rate is a tough number for any company to overcome. But, with simple steps for a well thought-out implementation plan, anyone can harness the full potential that a CMMS can bring to an organization.
The following is an introduction to the steps you can take to ensure your CMMS implementation is a success.
1. Determine the scope of your project
Rushing to purchase a CMMS package often leads to a rush to implement. Stop and think before you buy. One of the top five reasons for implementation failure is wrong CMMS selection. You need the right CMMS for your application, and the scope needs to be defined before you select the package.
What exactly are you looking for your CMMS to do? What modules are critical to your business now: equipment, preventive maintenance? Can some modules such as purchasing wait a while? How do you see your company using CMMS after two years? How about after five years? Will you be interfacing it with other systems or using mobile technology in the future?
2. Get management commitment
Often, executive management doesn’t have a clear concept of CMMS and what types of initial and on-going resources must be committed to the project. Aside from the software acquisition cost, there are on-going costs for maintenance, training, data gathering and data entry to name a few.
Make sure these costs are included in the project estimate to give upper management a full picture of the time and budget required for your project. This will help you to receive their commitment for the full project.
3. Plan your project
Think about your implementation from start to finish. What are the key milestones? Determine who will be implementing CMMS, who will be gathering data and what types of data they will be gathering. Figure out a part numbering scheme, an equipment ID scheme, location schemes and labor and material charge accounts. Define code tables as a team during the planning phase such as work order type, work order status and completion remark codes. This initial planning can reduce a lot of confusion later.
4. Prepare for change
Don’t make the assumption that all your employees will welcome CMMS with open arms. Employees may see CMMS as a tool that will replace them in the future, and workers are fearful of anything that may put them out of work. It’s important to get all your employees involved early, publish informational memos about the change and hold question and answer sessions to get employee input so workers take ownership in the project and are excited about the positive changes CMMS can bring.
What obstacles can your current maintenance workers visualize in terms of data gathering and data entry? Are certain workers resistant to the change? One resistant worker now can cause unnecessary obstacles later leading to failure.
5. Training
CMMS is a sophisticated application and will require training for all employees using the system. Don’t make the mistake of underestimating your training requirements. There will need to be initial software training from the CMMS vendor, and on-going (or internal) training for your employees. Every organization implements CMMS in a different way, and your employees need training on your specific CMMS use.
Training employees on the way your company uses terminology is important – the distinction between a “bulb,” a “light” and a “compact florescent” may seem like splitting hairs now, but can lead to confusion and purchasing errors down the road. As new employees are hired, they will need training too. Timing of training is also important. Training should be done as close to the actual implementation as possible.
6. Data gathering, entry
Gathering all the necessary and useable data your employees will need to enter into the CMMS is usually the biggest culprit in any implementation project failure. Effectively gathering all the data will usually require 6-12 months of committed manpower resources.
Determining what data will be gathered such as equipment model, serial numbers, cost, warranty data, preventive maintenance, procedures, frequencies and parts information, and how that data will be gathered are key components of your implementation plan.
You’ve planned out your implementation, purchased your system and gathered your data. Having a solid plan for how to enter the data into the system will deter confusion later.
Initially, there is a massive amount of work required for entering all the data you have gathered. Who will do this job? There are outside contractors to consider, current employees to tap or temporary hires. Fortunately, this large amount of work needs to be done only once.
Next, you need to determine the best method of entering the necessary day-today information the CMMS will manage. Should an administrative assistant enter completed work orders at the end of the day or should each maintenance technician enter their own completed work orders? Think each possible solution out to determine the pros and cons of your specific situation.
7. Follow-up and continuous improvement
Don’t just use the CMMS as a recordkeeping tool to keep lists of your assets and their parts. Spreadsheets can do that. Make sure you know the full functionality of the CMMS, and plan ways to improve your use of it in the future. CMMS gives you the ability to look at a massive amount of data that can be tracked. Is someone looking at the data? How can you look at trends, analyze them and take corrective action?
For example, are there failures with a specific piece of equipment or a part? A CMMS can help you determine why those failures are occurring. Are you constantly monitoring and improving upon your maintenance operation?
Keep watching for additional information and strategies to use when following these steps for your successful CMMS implementation.
Kris Bagadia is a consultant and an educator with PEAK Industrial Solutions, LLC, Milwaukee, WI, (262) 783-6260.
Griežtai draudžiama paskelbtą mūsų medžiagą ir informaciją panaudoti arba platinti kuriuo nors pavidalu be UAB „Inobalt“ sutikimo, o jei sutikimas gautas, būtina nurodyti UAB „Inobalt“ kaip šaltinį ir nurodyti internetinę svetainę http://www.inobalt.lt. Dėl sutikimo gavimo, kreipkitės el. paštu info@inobalt.lt.
Efficient Energy Management, finally standardized. ISO 50001 standard provides concrete steps, like step by step to reduce energy consumption and CO2 emissions into the atmosphere.
The energy management standard is divided into next steps:
1. Energy efficiency analysis.
Carry out energy audit of the cost of traffic to determine the current position and record energy costs.
2. Visualization and measurements.
Next important step in the development of efficient energy use visualization and measurement. Continuous monitoring of energy costs and creates a visualization of the possibility of system optimization and improvement.
3. Process optimization.
This is a real action or a process known as the "who, where, when" improving the energy efficiency of resources, the current time, the equipment and technological process.
4. Continuous process control.
Regular improved process control, allows to maintain the level of energy efficiency. Permanent control of the use of data collection and transmission equipment and software.
We offer a measurement system that will support the implementation of energy management standards, which comply with the ISO50001 standard and reduce energy costs.
Griežtai draudžiama paskelbtą mūsų medžiagą ir informaciją panaudoti arba platinti kuriuo nors pavidalu be UAB „Inobalt“ sutikimo, o jei sutikimas gautas, būtina nurodyti UAB „Inobalt“ kaip šaltinį ir nurodyti internetinę svetainę http://www.inobalt.lt. Dėl sutikimo gavimo, kreipkitės el. paštu info@inobalt.lt.
Exhibition Tech Industry 2011
With rising interest in energy consumption and energy management in Latvia, the focus on precise and reliable measurement increases. Therefore Inobalt, exhibit their proved products for energy saving, optimization of process and control systems, temperature measuring, dew point measuring, pressured air consumption and leakage detection as well as the brand new intelligent data acquisition device Expert.
From Noveber 24st to November 26st TechIndustry fair in Ryga presented an international specialized forum for mechanical engineering, metalworking, automation, electronics, electrical engineering, tools and innovated technologies. Inobalt gathered lots of interest with proved and new products. Especially the reliable and precise products for energy saving solutions, solutions for optimization of process and control systems, temperature measuring, dew point measurement, compressed air consumption and leakage detection attracted lots of attention. But hidden star was the new intelligent data acquisition device Expert, the newest product of Inobalt. With its extensibility for up to 30 different sensors, the easy-to-use software and wide range of measurement- and analyze-options the Expert builds the perfect basement for detailed energy-management systems.
Company Riveja at conference about energy efficiency and solutions for energy saving
22.02.2012 company Inobalt participated at conference about energy efficiency and solutions for energy saving in Lithuanian conference center Litexpo. The conference was organized by Lithuanian electric power distributor LESTO and business newspaper VERSLO ZINIOS. There were about 180 participants from different industrial companies.
Company Inobalt presented products for measurement gas and compressed air: leak detector, mobile data logger and sensors for flow, pressure, humidity and current, software for energy data monitoring and management, electric actuators.
Inobalt attained big interest for exhibited energy saving products.
Company Inobalt at exhibition "Ka pasesi... 2012"
Company Inobalt participated at International agriculture exhibition "Ka pasesi... 2012". Company Riveja exhibits proved products for energy saving, optimization of process and control systems, temperature measuring, dew point measuring, pressured air consumption and the brand new intelligent data acquisition device Expert.
International agriculture exhibition "Ka pasesi... 2012" on 29-31 of March took place in Aleksandras Stulginskis University in Kaunas, Lithuania. It was seveteenth spring and thirty fourth of the total exhibition organized in the University. There were participating 260 companies and organizations, about 350 small farmers, manufacturers and sellers. 85 thousand visitors attended exhibition. Many visitors came from neighboring countries: Latvia, Estonia, Belarus, Ukraine and Poland.
The latest technologies at the exhibition also presented companies supplying the farm equipment and livestock products. Also plentiful was the heat supply equipment, fertilizer and plant protection products, horticultural and floricultural gardening exhibitions.
Attendance to all the events that took place in Aleksandras Stulginskis University was free.
Riveja Ltd is changing company name to Inobalt Ltd
We would like to inform you, that from 21 September, 2012 the company RIVEJA Ltd officially changes its name to INOBALT Ltd.
Company's code, VAT code, registration address, contact phones, bank account details remain unchanged, except e-mail and website addresses.
All collaboration contracts signed remain valid, no need to resign.
Starting from the 21 September, 2012 we kindly ask you to change the company name in your systems.
INOBALT Ltd
Registration address: H. Manto str. 84-310 Klaipeda, Lithuania LT-92294
Company reg. No.: 141319369
VAT No.: LT413193610
Account: AB SEB LT607044060000544837 SWIFT/BIC: CBVILT2X
Ph.: +370 612 22499
E-mail: info@inobalt.lt; rolandas@inobalt.lt
http://www.inobalt.lt http://www.inobalt.com
Exhibition Tech Industry 2012
Exhibition „Tech Industry 2012" presented about 250 companies from such countries as Latvia, Lithuania, Estonia, Finland, Sweden, Poland, Italy, Germany, Russia, Ukraine, Belarus and other countries took up two exhibition pavilions to show advanced metalworking and industrial equipment in operation and showing mechanical engineering equipment and materials, air-flow and hydro technologies, industrial metalworking products, automation and control systems, hydraulic equipment, power tools, measuring equipment, electronic and electrical equipment, gas supply equipment, as well as other equipment, materials and technologies.
Participants demonstrated a large number of new yet unseen equipment, tools and materials that can be implemented and used by both industrial manufacturers and service providers as well as by a vast range of manufacturing companies to modernize and streamline production process and make it more cost-effective.
The INOBALT was represented by numerous innovations at the fair. For example, the new multi-instrument mobile data logger was presented at the exhibition.
For the first time, all measurements can be captured, displayed and stored in a logger. Also, all energy/consumption meters for compressed air, gases, water, electricity, heat quantities, steam, etc. can be recognized and analyzed. This greatly simplifies the energy management according to DIN ISO 50001.
The INOBALT showed mechatronic products too. There were demonstrated innovative solutions of ball and lead screws, gearheads, linear modules, actuators, CNC solutions etc.
Have a question?
{rsform 2}
LogMessage5000 – New Data logger with galvanic isolation
The new LogMessage 5000 data logger enables data acquisition from 16 differential analog inputs with galvanic isolation of up to 650 VDC. High-level isolation is particularly important when acquiring measurements from voltage-carrying components, such as in the product testing of household appliances or electric motors.
Each of the LogMessage 5000's analog inputs can be separately configured. For temperature measurement, any type of thermocouple can be used. The LogMessage 5000 is equipped with linearization curves for all thermocouple types and has pre-installed reference points. Any thermocouple can then be connected and used immediately.
Pt100 and Pt1000 sensors can be fed directly from the LogMessage device via a 4-wire connection. Analog inputs can be used to also measure mA or mV signals. Scaling is performed immediately according to the required measurement unit.
Data can be transferred online to a PC via the LogMessage 5000 LAN interface. The LAN interface is also galvanically isolated as are the power supply and all other interfaces - by up to 1000 VDC.
The LogMessage 5000 is equipped with an independent data storage capacity of up to 250 million measurement records. This gives improved data security and reliability over PC-based systems.
Each measurement record is recorded with a time and date stamp. Up to 10 measurements per second per channel can be recorded. The data is then evaluated using the ProfiSignal Go software included with the LogMessage 5000.
News
Radiometric IR inspection for flight applications
Market innovation! | INOBALT PI LightWeight kit performing IR flight |
|
|
|
|
Fly with us! Let us advise you personally: Tel: +37061222499 |
Further information |
PI LightWeight Datashheet PDF >> | |
PI thermal imager Product brochure PDF >> | |
PI series Product page >> |